NACE-CERTIFIED
EXPANSION JOINTS
FOR AN OIL REFINERY
Oil refinery
Sweden
EN14917 + NACE
Belman has designed, manufactured and tested 12 NACE-certified Expansion Joints for a flare line at an oil refinery in Sweden. The media in this flair line is potentially extremely toxic and constitutes a critical safety threat in the event of emission. This places very high demands on all the components in this part of the pipeline.
Client challenge – critical media demands specific NACE requirements
The client needed to relocate its flair line to make room for a new plant for the production of biogas. The media used for the flair line is capable of developing H2S (Hydrogen sulfide, also known as sour gas), which is extremely flammable and highly toxic and thus constitutes a significant risk to human safety in the event of emission. Another critical issue is that this H2S gas corrodes metals in the equipment installed in the pipeline, as the gas makes the material friable (this is known as HCC, Hydrogen Corrosion Cracking). All these critical issues mean that all components installed in this kind of application need to be NACE-certified. The client therefore needed a supplier able to provide NACE-certified expansion joints and most importantly, who was experienced in this line of work and flexible to meet the very specific requirements.
BELMAN’S SOLUTION
Belman, together with our partner in Sweden, worked very closely with the client’s engineering team from an early stage of the project to ensure a robust, durable, safe and cost-efficient NACE-certified Expansion Joint solution that met the requirements for their application. The solution was to use Hinged Expansion Joints that could absorb the angular movements generated by the operation, as this design resists the pressure thrust from the piping system as well as reducing the loads on the fix points. As a Hinged Expansion Joint solution is often a heavy construction, Belman engineered a cost-efficient lightweight design with special consideration for the durability of the Expansion Joints. The final product was an Expansion Joint solution that meets NACE requirements.
NACE-certified materials and welding procedures
The risks involved in working with H2S gas, together with the application, meant that any expansion joints used in the flair line would require NACE-certified materials and welding procedures. The materials used for the Expansion Joint needed to have a special chemical composition that met NACE requirements. As the material hardness after welding was an issue, special welding procedures (WPS and WPQR) were required. Belman is very keen on the client achieving the best solution with the smoothest work process, which is why we always make/adapt our welding procedures (WPS and WPQR) to NACE requirements. In order to achieve the best solution for the client, it was agreed that we would use free issued materials for the pipe ends delivered by the client. Belman arranged the pick-up of the materials. A silicone aluminium coating system was applied to all the carbon steel parts of the NACE-certified Expansion Joints which would be resistant to the surrounding environment. Comprehensive testing and extra tests were made in accordance with NACE requirements (including HIC testing as per NACE and impact testing up to -46°C). The Expansion Joints are a CE-marked solution according to category III PED 2014/68/EC Module H.
Involving Belman at an early stage to achieve the best flexible solution
Since 1994, Belman has customised and engineered Expansion Joint solutions for clients in many different industries worldwide. Many of these Expansion Joints have been for onshore and offshore oil & gas applications designed according to many different norms and standards. Belman’s highly specialised engineers are able to produce Expansion Joints that meet every technical demand the client may have. This is why so many clients turn to Belman to ensure their special requirements are met. They often involve Belman at an early stage to achieve a safe, durable and cost-efficient Expansion Joint solution and an improved total cost of ownership (TCO). Read more about Belman’s engineering and troubleshooting here: Design & Engineering at Belman
As well as our Belman Design services: Belman Design website
DESIGN FEATURES
Design parameters of the NACE-certified Expansion Joints :
Type: Hinged expansion joints • Quantity: 12 pcs. • Dimensions: DN 1200 • Installation length: 1280 mm • Medium: Flare Gas, CO2• Design pressure: -0,3/3,5 barg • Design temperature: -46°C /+304°C • AN: +10/-10° • Bellow: 1.4541 (AISI 321) • Inner sleeve: 1.4541 (AISI 321) • Pipe ends: SA-516 gr. 70 • Hinges and lugs: 1.0565/1.1106 (P355NH/ -NL2) • Design code: EN14917 + NACE
CLIENT BENEFIT
- A verified and tested Expansion Joint solution that meets NACE requirements
- Expert assistance on the design and material selection for the Expansion Joints
- Safe absorption of movements in the flare line
- As part of the pipeline design and risk assessment, the high-end engineered Expansion Joints release stresses in the system, thereby reducing the loads on piping, equipment and fix points for a safer operation
- The considerable know-how of an experienced manufacturer
- An Expansion Joint that is designed to work under specified operating parameters for reliability
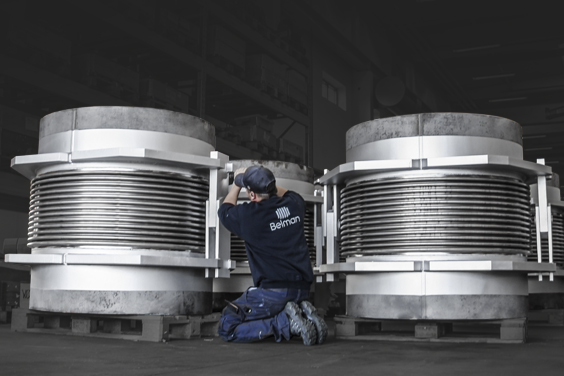
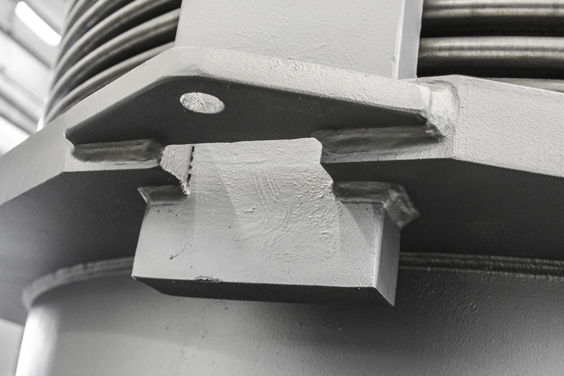
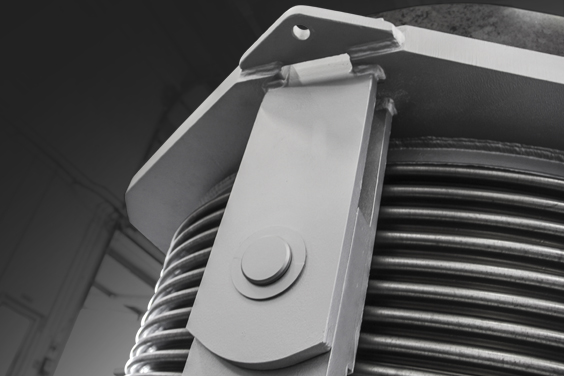
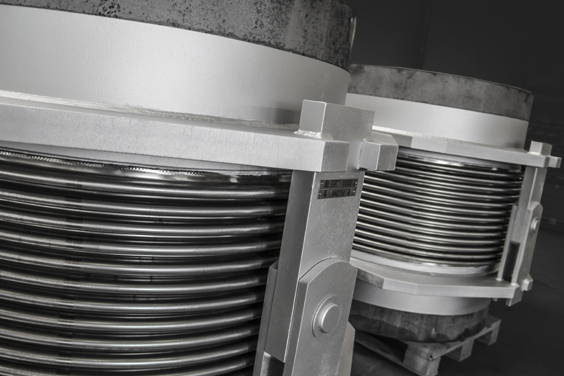
RELATED INFORMATION
TECHNICAL information
- Technical information on hinged expansion joints in the Expansion Joint Catalogue
page 29-30
- See here how Hinged Expansion Joints absorb movements:
REFERENCES
Total Fina Elf • BP • OMV • Gunvor Petroleum (Prev. Kuwait Petroleum Europoort B.v (Q8)) • Shell • Statoil • Rosneft • Enap • TOR • MOL • Chevron • Eni • Murco Petroleum Limited • Linde Ag • Qapco • Lukoil • Preem • Total • PKN Orlen • Saudi Aramco • KNPZ • Maersk Oil • Tatneft • Ceylon Petroluem • Termo Petroleo • Repsol • Equinor (Statoil) • Novatek • Valero • China National Petroleum Corporation (CNPC) • Ineos • National Refinery • Valero • GE Oil & Gas • ExxonMobil • Sinopec • Petrogal • NOV • Ruhr Oel •